What Will the Rise of Electric Vehicles Mean for Metalcasters?
This article offers a look at some possible influences of the electric vehicle platform on metalcasting in the coming years, including the forces pushing the world toward EVs and away from internal combustion engines, and issues that must be resolved as industry prods consumers to embrace EVs.
Automotive manufacturers have decided it’s time to offer consumers more electric vehicles (EVs), and as a result, fundamental change could be coming to automotive industry suppliers, including metalcasters.
EVs are at the confluence of inexorable forces: 1) the recent exponential growth in technology and its applications to manufacturing and 2) the exhaustion of innovative options for the internal combustion engine (ICE) cars. After 100 years of ICE dominance and the “brotherhood of muscle,” automakers have clearly signaled they want to transform their manufacturing focus to the new EV platform.
Along with exponential technology, two other hard trends are relentlessly pushing automakers toward EVs: increasing regulations and inexorable demographics, meaning, the workforce is being remade because of boomer retirements.
For decades, metalcasters sold millions of cast components to automobile manufacturers. The weight of the average ICE vehicle is about 4,000 lbs. Six hundred of those are castings. What happens when the customer chooses to go all in for a brand-new automotive platform that requires only a fraction of that 600 pounds?
EV Platforms and Technology
New technology often disrupts businesses already experiencing success. Successful businesses are prone to resist disruption. They are successful now, and they don’t like too much boat rocking. These businesses may embrace the productivity offered by the new technology, but often they fight to maintain their position through the same decision-making that put them in a good position. This can be the path to ruin. The classic examples are carriage manufacturers, when “horseless carriages” began to supplant them, or Kodak, the ruler of film photography world, turning its back on the digital photography revolution.
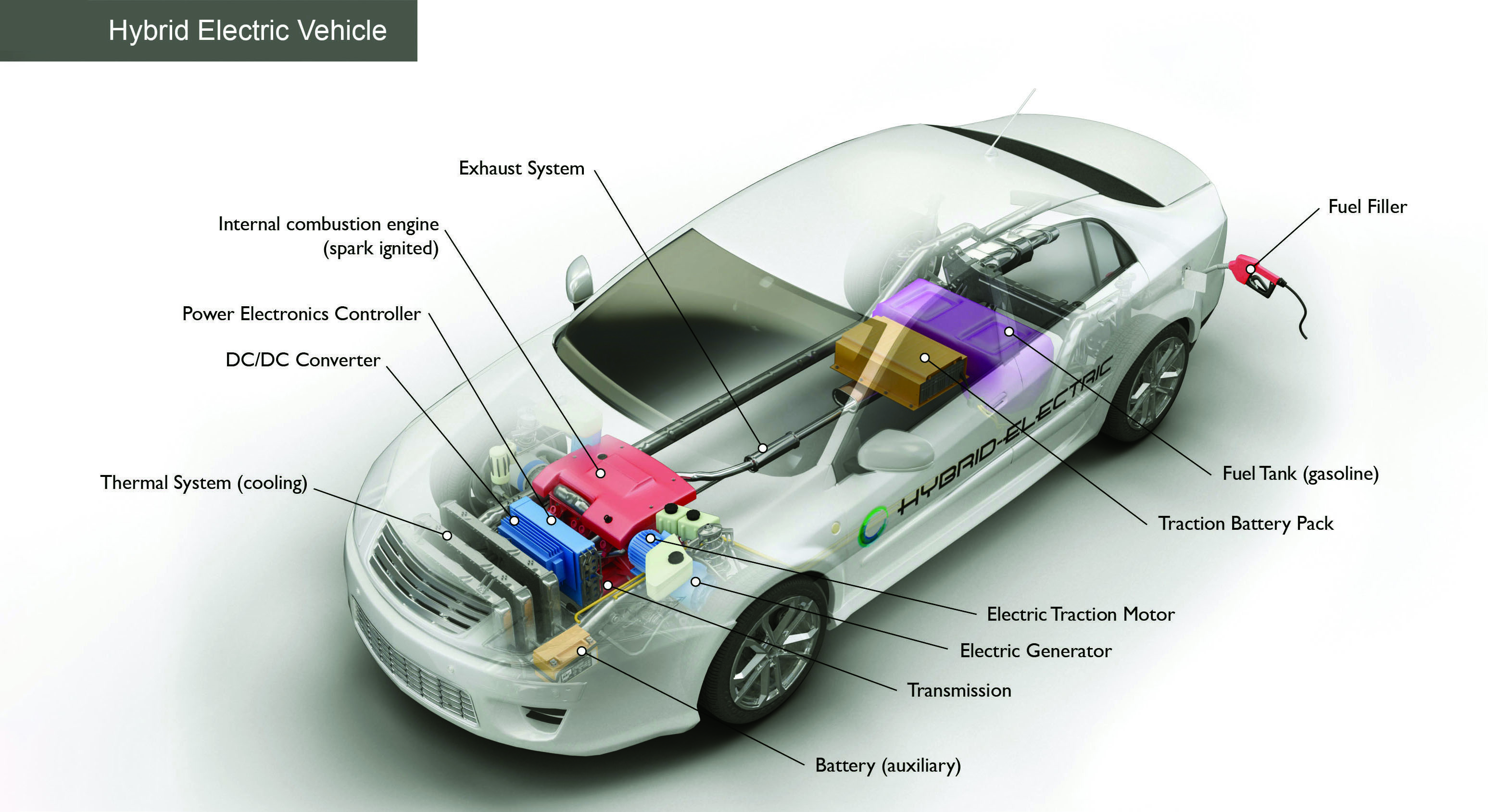
The case of Nokia vs. Apple is a more recent example. In 2007, Nokia sat atop the mobile phone universe. But, as one business analyst said, it was the largest dumb phone maker. That year, smart phones were introduced.
“Nokia tried to respond to the iPhone the only way it knew how–by taking its Symbian operating system designed for low-IQ phones and trying to remold it into a smartphone operating system. That attempt failed miserably,” according to Vitaliy Katsenelson of ContrarianEdge.com.
Knowledge of the existing platform, ironically, is often not an advantage. “When you are in the middle of a transition from one domain to another, your knowledge of the past domain may cloud your vision. You’ll be seeing through the lenses you’re used to wearing,” Katsenelson writes.
This problem of not striving to understand the possibilities of the radically new has always been part of human nature. Some existing auto manufacturers are undoubtedly going the route of Nokia. Others will find a way to have more success with the new EV platform. Tesla started more like the Apple iPhone, from a blank slate, rather than like Nokia, which tried to make its existing platform function in a way it never could.
Consistent with the story about Apple and Nokia, long-time auto industry observers say it’s a mistake to view an EV as an ICE vehicle with merely a different powertrain. An ICE powertrain has about 2,000 parts, many of which are cast. The Congressional Research Service confirms EV powertrains will have 20 parts. Those parts could be metal, but not much, if anything, will be made in a foundry.
The standard estimate of 600 pounds of castings in an average automobile will be dramatically reduced with electric powertrains.
Unfortunately, that might only be the beginning of the bad news for metalcasters.
A Detroit insider and advocate of Corporate Average Fuel Economy (CAFE) standards, with more than three decades of industry experience, explained that the push to lightweight resulted significantly from automotive physics, which is “all about aerodynamics and mass.” Now designers are poised to go much, much further than ever before. Every part of the vehicle will be extensively reviewed for redesign. All materials used in automobiles are liable to be new and improved in the EV platform. That includes all auto parts, including cast parts now used in brake systems, suspensions, wheels, etc.
The new EV platform has “skateboard” architecture used by Tesla vehicles. In fact, one automotive expert explains that EVs can be built to customer specifications. The words to describe this are “bespoke,” and “tailor-made.” EVs can be built with a lower center of gravity and the cabin can be moved forward with more passenger and more cargo space, so the car will have a “frunk,” or front-loading trunk. EVs can even have in-wheel electric motor systems. Manufacturers in the auto supply chain will have to rethink their business models.
Many foundries have a business model they have rightly felt was “hermetically sealed” from the automotive supply chain. Regardless of whether auto manufacturing was experiencing boom or bust, those foundries were not seriously affected. But it will be much more difficult to remain unaffected as the EV market grows. When fewer castings are required in an industry as dominant as auto manufacturing, competition for contracts will increase.
For instance, economics might drive a large production foundry to underbid a smaller job shop for smaller contracts as the bigger business stays afloat. Then business improves. The production foundry suddenly has more orders than it can or wants to handle, and it sends smaller contracts back to the job shop. All things being equal, this give and take can be repeated, with contracts going back and forth. What happens to this process when a massive number of castings are no longer demanded by the market? Will production foundries permanently absorb the smaller contracts that have traditionally belonged to job shops? Will there be less work for all foundries as the market seeks equilibrium?
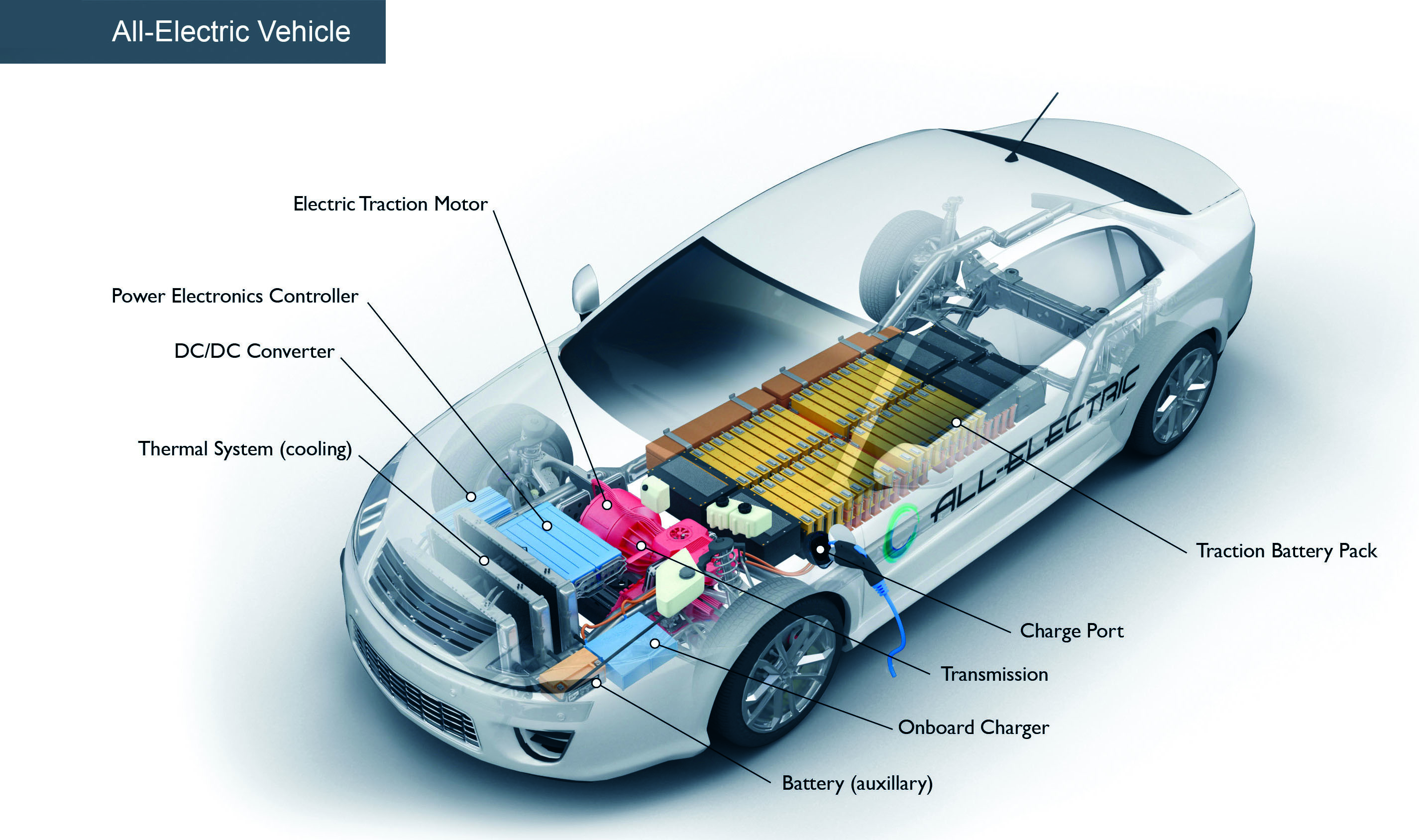
Incentives for Manufacturing EVs
The attraction to new technological possibilities is a strong motivator. Others are concerns about climate change and the legal requirements of CAFÉ regulations, and the largest automobile market: China. The metalcasting industry continues to be affected by all these.
After 100 years of refining and improving ICE technology and feeling like there is little room for technological improvement, why wouldn’t the auto market want to make a new product? They must believe that a totally new platform will bring similar financial benefits as the advent of the Ford Model T, when Henry Ford became fabulously wealthy.
EVs are quieter, smoother, and lower maintenance than ICEs. If you put yourself in the boardrooms of major automakers, doesn’t a complete platform swap sound like a plan for long-term financial health?
The world saw the allure of new tech in personal vehicles when on Nov. 21, 2019, Elon Musk introduced Tesla’s Cybertruck. By Nov. 27, Tesla claimed it had 250,000 pre-orders for a thing that looks more like Hollywood transportation for Sigourney Weaver fleeing blood-thirsty aliens than something driven by your friendly neighborhood handyman.
Auto manufacturers also know the victory stories of Apple, digital photography, and horseless carriages. They also have studied the failures of Nokia, Kodak, and buggy makers.
Metalcasters have long been affected by CAFE regulations and the attendant climate change concerns. These regulations were elevated in July 2011, when President Obama struck a deal with large car manufacturers to increase CAFE requirements to 54.5 miles per gallon. This covered automobiles and light-duty trucks by model year starting in 2025.
The onerous tightening of fuel economy regulations has been resisted by the Trump administration, and the issue has not been resolved. Odds might be in favor of the policy set in 2011. Detroit sources believe Trump’s action will result in lawsuits to maintain Obama’s standards, but like most legal matters, it’s guessing.
It’s not guessing to say the largest auto market on earth is driving the world to EVs.
For the automotive supply chain, the market in China may be the most significant driver toward EVs. According to data company Statista, in 2018, China produced almost 28% of the world’s passenger vehicles, and the U.S. came in second with 13%. After the U.S. came Japan, Germany, India, South Korea, and other smaller producers. China wants all its cars to be EVs.
As with all things EV and China, there are more complications than you might expect. In October 2019, The Wall Street Journal ran this headline: “Who Willed the Electric Car? China, and Here’s Why.” The sub-headline expressed one of the contradictions many observers have noted: “Electric vehicles that derive their power from dirty energy aren’t necessarily better for the environment, but they are better for Beijing.”
According to NPR, “China is building or planning more than 300 coal plants in places as widely spread as Turkey, Vietnam, Indonesia, Bangladesh, Egypt and the Philippines.” Which improves China’s carbon footprint, but not the planet’s.
The crux of China and EVs is more about economic hegemony than air quality, according to the Wall Street Journal: “More than that, though, Beijing wants to dominate tomorrow’s car industry. China’s opening to the West came too late for it to be a major exporter of internal combustion engine vehicles, but it has made aggressive moves to dominate battery production, including securing sources of key metals. Through lavish subsidies it already has by far the world’s largest domestic EV market.”
The incentive to be the global leader in such a critical industry as automotive manufacturing could be stronger than the motive of clean air. U.S.-based automakers want to be part of the massive Chinese market.
UNRESOLVED ISSUES FOR EMBRACING EVs
Jobs
Job losses are not only a disadvantage to the larger economy, but obviously a disadvantage to those who lose their jobs. In late November last year, headlines said Audi was about to slash 9,500 jobs in German auto manufacturing but will add 2,000 jobs for EV production.
In an interview published earlier in 2019, Morgan Stanley’s Adam Jonas said there are about 11 million employed in the global automotive supply chain, and 3 million could lose their jobs as a result of electrification. These job losses will have a ripple effect that will include metalcasters.
But let’s look at the job-creation side of technological advance. Remember Nokia? According to Statista, when the iPhone was introduced in 2007, Nokia had 112,000 employees. In 2018, it employed 103,000. But Apple has grown from a 21,000-person company to one with 132,000 employees. Despite the loss of jobs for Nokia’s phones, that is an aggregate job gain globally of 77,000 from technological progress.
Specific job losses resulting from reduced powertrain jobs are not good news, but they appear to be inevitable. The hope is that disruptions result in new opportunities, as illustrated in the numbers above. New tech across personal vehicle platforms will create jobs in new areas and opportunities for forward-thinking metalcasters. The key is for manufacturers to find those opportunities and exploit them.
Foundries will be affected, but others much more so. New opportunities will be sought by those in the used ICE car markets, repair mechanics, and body repair shops. Parts distributors, like AutoZone or O’Reilly Auto Parts could go the way of Blockbuster and Borders.
EV Range
A company investing in a network of charging stations, EVgo.com has a map on its site of charging stations locations. The convenience of the existing infrastructure to deliver gasoline to tens of thousands of retail locations clearly remains superior. As with many things we think the future holds, we don’t know how quickly adequate charging infrastructure will be created across the country or in our local communities.
The EVgo.com website asserts, “Charge your car in minutes, not hours.” The time necessary for charging an EV is better analyzed with numbers. Tesla says it will soon charge batteries in 10-15 minutes for a range up to 350 miles. The Tesla Model S has a maximum range of approximately 337 miles, according to Tesla and Tesla owners.
The lesson is EV technology is improving by leaps and bounds. It’s prudent to assume the research and technology will keep improving, and the switch to EVs could be sudden and spectacular. Manufacturers who incorporate the hard trend of technological advance into their plans will have the best chance of success.
Emissions and the Cost of Fuel
Regarding tailpipe emissions, EVs win in a landslide. Even when the electricity used to charge EVs is produced by coal, EVs are better for air quality than ICEs. For the moment, EVs also have a lower cost of fuel, as seen in this chart from the Congressional Research Service. This assessment provides a look at electricity costs now.
But there’s an economic conundrum here. Does anyone really think the cost of electricity will remain static when thousands, or even millions more drivers are trying to charge their vehicles quickly? Increased demand means increased price.
The U.S. grid is notoriously unsecure. Hacking the grid would hinder oil refining and distribution of gasoline, but it would shut down charging for EVs.
For metalcasters, what will higher electricity costs mean for an already constrained and expensive energy resource? Renewables have made great strides in recent years, but there is a long way to go before we can drop fossil fuel-produced electricity.
Costs and Batteries
In August 2019, qz.com reported that the average cost of the most popular vehicles in the U.S.—70% of the market—rose to $36,000, while the EV price, like most things technological, maintained a downward trend.
Still, as Autowise.com puts it, “There is no disputing this fact. Electric is expensive.”
The reason is fuel storage. “The batteries require lithium, which is a rare metal that can only be mined in a handful of countries. They’re expensive batteries to produce, and heavy too. The battery is only one of many expensive features of an electric car,” according to Autowise.com.
Like other, newer technologies, battery problems will be attacked, researched, and solved in the coming years. How fast the necessary upgrades can be implemented is not predictable, but even cursory research shows that those who love the idea of EVs think the improvements will be next year; those less enthusiastic believe it will be longer, perhaps much longer.
As with all problems resulting from technological disruption, there are opportunities. Standard ICE lead-acid batteries pose recycling challenges, but lithium-ion batteries used in EVs can be recycled into other batteries at a rate as high as 95%. That’s a good thing, since disposing of the batteries is environmentally undesirable. More technologies and new businesses will develop around wider use of lithium-ion batteries.
There is also a fascinating possibility of solid-state batteries in a few years. For the moment, ICEs will hold their appeal for the cost-conscious.
Conclusion
EVs are here and more are coming. The march of technology and global auto manufacturing ambitions are propelling the adoption of the new EV platform.
There are problems facing the wide adoption of EVs. These include charging times, charging locations, range, cost per vehicle, battery issues (for now), job disruption for some, and other things. But the advantages of low maintenance and eliminating tail pipe emissions, and noise reduction could more than counter most disadvantages.
How fast will the change to EVs occur? Myriad variables make the answer to this question an answer metalcasters recognize: “It depends.” A return to rigorous pursuit of CAFE by EPA could motivate auto manufacturers, as could sudden changes in technological capabilities. The problem of a diminishing employee pool is not just a problem for metalcasters, but in all manufacturing. EV manufacturing will require a smaller workforce than we now have on assembly lines.
According to the U.S. Energy Information Administration (EIA), there are currently about 370,000 electric vehicles, which includes cars, light trucks and freight trucks. They represent 0.1% of the total stock of vehicles (253.7 million cars). By 2033 there will be an estimated 13.5 million electric cars, light trucks and freight trucks on the road. They will represent 5% of the cars/light trucks and 0.5% of freight trucks, excluding hybrids.
This might sound as though metalcasters in the ICE supply chain have very little to be concerned about, and that the rise of EVs will not disrupt metalcasters in the near future. As the industry continues to consolidate and modernize, it might be time to reflect on Benjamin Franklin’s truism that “an ounce of prevention is worth a pound of cure.”
However individual metalcasters decide to see the future, the time for serious assessment of the impact of EVs has arrived.
This article and the presentation derived from extensive research and three years of conversations with AFS Corporate Members and interviews with outside sources. It was first given as a talk at the AFS International Ferrous Melting Conference, Oct. 29-Nov. 1, 2019, in Nashville, Tennessee.
Click here to see this story as it appears in the February 2020 issue of Modern Casting.