Automating Metalcasting Operations
Metalcasting facilities can improve productivity and solve issues labor shortages by automating.
Metalcasting facilities hold several opportunities to improve production efficiency, casting quality, and worker safety with automation.
Automating the Grinding Room
The grinding area of a foundry is notoriously one of the most labor-intensive departments on the production floor. Foundry managers are keen to automate grinding—for the right price and setup.
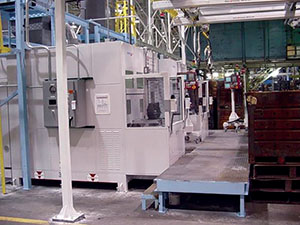
“In some foundries, around 60% of the workforce is in the grinding room. Entry level foundry jobs have the biggest turnover.” said Don Laundre, Regional Sales Manager for AFS Corporate Member Sinto America, Inc. (Grand Ledge, Michigan).
Manual grinding is not just a hard job, it can be the source of inconsistent quality and production due to human error.
The options to automate grinding include what Laundre calls “grinders in a box.” These are self-contained machines in which a part is set into a fixture and then the grinding is automatically performed in a set of steps as programmed. Another option is to set up a robotic cell where a robot takes a part to different grinding stations, or the robot can take the tool to the casting.
Self-contained automated grinding machines normally have faster cycle times with more accurate results. The casting is in contact with the tool the majority of the cycle and is in position and supported during the full grinding cycle. Self-contained automated grinding machines also save space but the casting sizes are limited (usually to 36 in. in diameter and up to 350 lbs.). Tool variety can be limited to two or three configurations as well, unless a quick-change tool is used.
Modular cells can work with small or large casting sizes and different tool configurations such as finishing belts, grinding wheels, drilling and gaging; however, tooling will be dictated for that casting per that casting family and increases the total cell cost. Plus, when castings are gripped internally or externally, there is the possibility of slipping during grinding. With both self-contained and modular cells, the workers environment is safer and productivity increases.
“The benefit of adding automation in your cleaning room is the increased throughput. You have production control,” Laundre said. “You know the machine is always going to grind. It shows up every day and there is no fatigue factor.
Laundre suggests when entering the automated grinding arena, a foundry should start small and then invest in additional grinding processes.
“The price tag for a complete cell is pretty high,” he said. “Get the first machine in there, get it debugged and running, and then move on to phase two or three or four. Walk before you run.”
Once the first machine or phase is running smoothly and efficiently, foundries can move on to the next phase. Sometimes the second phase gets moved up in the timeline after the success of the first phase becomes apparent.
“These grinding cells can carry price tags of $300,000 to $500,000, and customers don’t always see where the initial payback is.” Laundre said. “It’s not just cost that gets saved. It is more accurate grinding, safer working conditions, and better productivity.”
Pouring With Robots
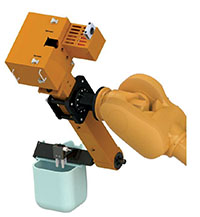
Automation removes human error from the metalcasting process. It also removes humans from areas that are hard on the body. As finding and retaining dependable workers continues to be difficult in the age of baristas and coders, pouring molten metal in a foundry is beginning to be a job that nobody wants to do.
“Some foundries are automating for that reason alone,” said John Kuhn, foundry automation specialist at AFS Corporate Member Rimrock Corp. (Columbus, Ohio). “And if you are pouring above 50 lbs., you need two people pouring a single ladle.”
Many options are available to automate pouring, from dosing furnaces to robots. Robotic pouring cells work well when flexibility is needed. Typically, they are stationed near molding lines and ladle out the molten metal as the molds move past, or they can be set up in cells and pour various molding stations around the robot.
Foundries have a variety of choices when setting up a cell, from the capacity of robot to the size of the pouring cup.
“Robotic pouring is very consistent. It goes to the pre-programmed place and pours the same speed and amount, every time,” Kuhn said. “That gives you the ability to tweak and improve the system slowly by looking at your casting results. You are not depending on a person to do the same pour every time.”
In robotic pouring, a 7-axis robot travels over the crucible or reverb and uses a laser or probe to sense the metal level. This tells the robot how far down to bring the ladle to pick up the appropriate amount of metal to be poured. With the metal in the ladle, the robot moves to the programmed molding station to pour.
Kuhn said a typical cycle time for a robot to ladle and then pour a mold is around 30 seconds. Some higher- production foundries have opted for two robots in a single station for a faster cycle time. Programming the robots can be simple too, Kuhn said. The robots he works with uses the same pouring program as the simpler one-axis ladles that have ladle angle and speed adjustments.
“The operator picks the speed and angle to pour, and then tweaks it without being a programmer. They just have to know how a ladle works,” Kuhn said.
When picking the ladle for the robot, foundries should be careful about the size, Kuhn said. The process becomes inefficient if the weight being poured isn’t fairly close to the size of the ladle. For instance, if the robot is equipped with a ladle rated for 50 lbs., a good range is 30—40 lbs. poured. Pouring 5 lbs. with a 50-lb. ladle is inefficient and causes oxide to build up.
The robotic cell also requires a safety fence around the area so it and the employees are well protected. The area to be fenced can take up a considerable area, so available floor space is required.
Robotic pouring yields cost savings stemming from reduced labor, quality improvement, and safety improvement.
“Usually foundries achieve a ROI on the robotic pouring in two years or less,” Kuhn said.
Robotic Mold Milling
Demand for patternless molding has grown as applications for complex and specialized parts have increased. 3D printing molds has become an industry-accepted method for meeting this demand. Foundries, pattern shops and OEMs are taking advantage of additive methods to create designs that were previously uncastable. When it comes to 3D printing sand molds, the printers themselves remain a significant investment for foundries to bring in-house.
Another option is available for foundries that want to bring the patternless making in-house: robotic milling.
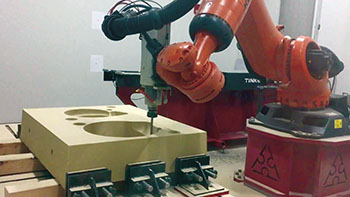
An example of a robotic mold milling cell consists of a six-axis industrial robot with an automatic tool changer, a base for clamping sand blocks up to 2000 x 2000 x 1000 mm and a programming software such as Mastercam/Robotmaster. According to Jonathan Tinker, lead project engineer of AFS Corporate Member Tinker Omega (Springfield, Ohio), this type of cell can cost about one-quarter the cost of a high-end 3D sand printer with a job box size of 1800 x 1000 x 700 mm.
Besides cost, robotic mold milling’s advantages include being able to use the existing sand and resin system already used in the production foundry and the flexibility to be used in a variety of cell configurations.
“It is more cost-effective than 3D printing, and it is quicker,” Tinker said. “It’s good for low production numbers—under 10 is really the strong wheelhouse—and larger castings.”
But the system does have its limitations. Hollow features are difficult and sometimes impossible. Intricate passageways and fine details are also not well suited for robotic milling.
“In an ideal world, a foundry would have one of each and do hybrid molds where the bulk of the mold is done with a robot so you are not spending a lot of time printing the block,” Tinker said. “But then you could print the core or mold inserts for the more detailed work. There is room for both to work hand in hand.”
In one such example, redesigning a printed mold as a milled mold led to a more than 4-times reduction in volume. The cope and drag were milled into one block of sand and then split, while the cores were printed for the interior features.
In another example, a mold with tight undercuts and an offset parting line for the gating system was going to be difficult to robotically mill. So 3D printed mold inserts and robotically milled molds were used together for an 80% reduction in 3D printing volume.
Click here to see this story as it appears in the October 2019 issue of Modern Casting.