R&D Pushes Industry Forward
AFS research projects spur industry development and drive new applications.
People have been making parts out of cast gray iron for centuries. In 1966, the material accounted for more than three-quarters of total global casting production. But a new material was created in the mid-1900s by researchers that opened new applications for the industry. Its usefulness as a strong, yielding material made its popularity so widespread that by 2016 it accounted for over one-quarter of total ferrous and nonferrous casting production.
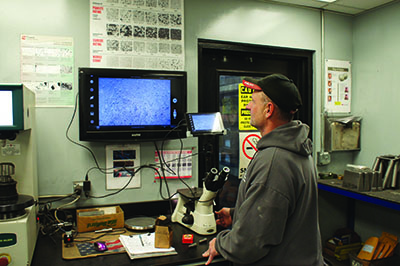
The material, of course, is ductile iron, and it is a prime example of the impact research and development can have on an industry.
Government agencies, independent associations, universities, and private sector businesses are working to push the metalcasting industry forward through research and development. These projects seek to improve manufacturing methods, diversify available materials, and create new applications.
The American Foundry Society (AFS) funds several research projects with allocated membership fees. These projects are selected and steered by volunteer-led committees and performed at properly equipped labs in foundries, colleges, and testing facilities.
AFS also collaborates with government agencies like the American Metalcasting Consortium and Defense Logistics Agency on research projects to advance casting engineering and design.
Following is a few of the current and recently completed projects that aim to find new and better ways to make quality castings as well as advance materials and processes to be used in new applications and markets.
Achieving Precise Low-Carbon Stainless Steel in Lost Foam
This project’s goal is to produce low-carbon stainless steel in the lost foam process. This steel casting market is primarily ruled by the sand and investment casting processes. Sand, while reasonably fast for delivery, especially in 3D-printed core and tool applications, is relatively imprecise compared to lost foam. Sand casting requires extensive machining of the casting and needs more weight for draft, stock, and molding dimensional issues. Investment casting, while precise, also has size and cost limitations. This research project will produce ASTM A351 CF8M stainless steel with 0.08% maximum carbon level in the lost foam process by understanding and implementing practices of bead selection, bead expansion, expanded bead density, permeability and fusion, coatings and their permeability, carbon-consuming additives, metal pouring rates and base composition and molding media refractoriness and permeability.
Improving Weld Repair in Aluminum 206 Sand Castings
Current practices to weld 206 alloy castings, particularly to repair through-wall defects or defect depths of greater than 0.25 in., result in unsatisfactory welds. Both 206 and 2319 weld rods are typically used for repair welding of 206 castings. A recent project to determine the effect of weld repair on the static and dynamic properties of A206 sand castings did not successfully produce welds of the desired quality. The work determined that the major problem is the chemistry of the weld wire used to make the welds. The two alloys currently used by AFS foundries (A206 and 2319) either produce inconsistent weld quality (A206) or low ultimate tensile strength (2319).
To mitigate the effects of weld wire chemistry and other variables on weld repair quality, a research project is using a set of statistically designed experiments to optimize a weld alloy chemistry and the welding parameters necessary for the successful weld repair of A206 sand castings.
Optimizing Gray Cast Iron Strength
AFS-sponsored research has defined which manganese and sulfur concentrations produce the best properties as pertains to gray cast iron strength. The potential improvement in strength is sufficient to significantly improve the marketability of iron castings.
Refining Investment Casting
AFS-sponsored research has demonstrated the importance of firing parameters on the thermo-mechanical properties of investment shells. With this knowledge, foundries are one step closer to achieving shells that provide sufficient mechanical strength with fewer layers. This could translate into a marked reduction in operating costs.
Harnessing 3D Printing for Lost Foam Tooling
Continuing AFS-sponsored research seeks to harness the power of 3D printing to expand the marketability and viability of the lost foam casting process. Lost foam tooling is, in general, expensive, with long lead times associated with the complexity of tool designs. This research is attempting to address this by demonstrating production of tools for high-mix, low-volume-production using 3D-printed aluminum.
It is expected that this research will result in halving of both costs and tooling-related lead times, allowing foundries to enter new markets.
Improving Steel Quality
Recent understanding on the effect of filling conditions on casting surface and performance of aluminum castings has resulted in design of new gating systems that eliminate damaged metal, greatly increasing casting quality and yield.
A research project is now underway to quantitatively evaluate the effect of different filling conditions on steel casting quality and mechanical properties. A series of test castings will be produced using different rigging systems commonly used in steel foundries. Filling of gating systems such as direct pour, horizontally gated, and bottom-gated systems will be designed using filling and solidification software.
The results of casting trials will be compared to the use of best-practices design involving bottom fill utilizing vortex gating. The objective will be to quantitatively compare casting metal quality and filling simulation results for a variety of filling conditions using a combination of optical metallography, automated nonmetallic inclusion analysis, and evaluation of mechanical properties.
Determining the Effect of Boron in Gray Iron
The use of boron-containing ultra-high-strength steel parts has been increasing in Europe and North America since 2007. Now, that steel is making its way into the scrap supply with unintended quality control consequences to gray iron foundries. Although boron is known to be a powerful carbide stabilizer, boron may also counteract the effects of pearlite stabilizing elements like Cu and Mn, resulting in ‘‘soft’’ pearlitic castings. It is debated what is the ‘‘safe’’ level of boron in gray iron castings or what effect boron has on the microstructure and mechanical properties.
A current AFS research project seeks to quantitatively evaluate the effect of different boron additions in the range of 8–60 ppm on the microstructure and mechanical properties of Class 30 and Class 40 gray iron.
The synergistic effect of boron and other alloying elements such as Cu and Sn trace elements such as nitrogen will be evaluated.
4 Ways to Apply AFS Research
Casting Process and Alloy Assistance
The AFS website provides tools to assist casting design engineers in selecting the best casting process for a potential component and provides casting alloy property data on many commonly used alloys. The goal is to give casting users, design engineers, and purchasers relevant and accurate information on casting capabilities and properties, providing easily accessible and retrievable information from a single site. Alloy property data can be quickly exported to a spreadsheet or FEA tools. The casting alloy and process selector, Casting Alloy Data Search (CADS), is located at www.afsinc.org under the Designers and Buyers tab or can be accessed directly at: www.metalcastingvirtuallibrary.com/cads/cads.aspx.
CastingConnection
CastingConnection is a private, professional, social network to connect, engage, and share critical industry information and best practices in real time. Through the Open Forum and sites devoted to special interest groups, AFS members gather to network via a comprehensive member directory and participate in focused discussion groups. AFS membership is open to any companies and individuals within the metalcasting supply chain, including equipment and service providers, foundries, academics, and end-users. Visit https://castingconnection.afsinc.org.
Online Library
The AFS online library contains current and historical articles and research papers about the metalcasting industry, including topics on metallurgy, casting processes, and material property data. The digital library is open to all AFS members. With a simple-to-use search, members have access to relevant technical and research articles and reports from all AFS published sources.
Author and summary information is available for viewing, and full articles can be downloaded. All technical and management papers published in AFS Transactions, from the first edition (published in 1896) to the present, are available, as well as technical articles from all AFS magazines. Hundreds of members have already leveraged this resource, conducting thousands of searches that span topics ranging from iron inoculation to silica exposure to gating and riser design. The library is located at www.afsinc.org under the Innovation & Management tab.
e-Learning
AFS offers a program that providing metalcasting-specific training, information, and education for the industry supply chain in a web-based format for a single access fee. The e-Learning program gives subscribing organizations full access to online modules for formal staff training on a wide variety of metalcasting topics. Individual e-Learning modules also are available a la carte. More information and a video demonstration are available at www.afsinc.org/e-learning.
Click here to see this story as it appears in the October 2019 issue of Modern Casting.