Responding to Changes in the Steel Scrap Stream
New elements present in the steel used in today’s cars means foundries will need to be more diligent in monitoring incoming charge material.
The trend in automotive manufacturing toward lighter cars has had a secondary effect on the steel scrap charge material used by iron foundries, and this trend looks to increase significantly over the next 10-15 years.
Through micro-alloying, advanced high strength steels have been developed and put into use to reduce the weight of a structural components in a vehicle. A part made with high strength steel can reduce the weight of a typical steel stamped part from 100 lbs. to 80 lbs. at about the same cost. Considering that replacing an existing steel part with aluminum saves weight but adds considerable cost, high strength steel is an attractive option for car manufacturers.
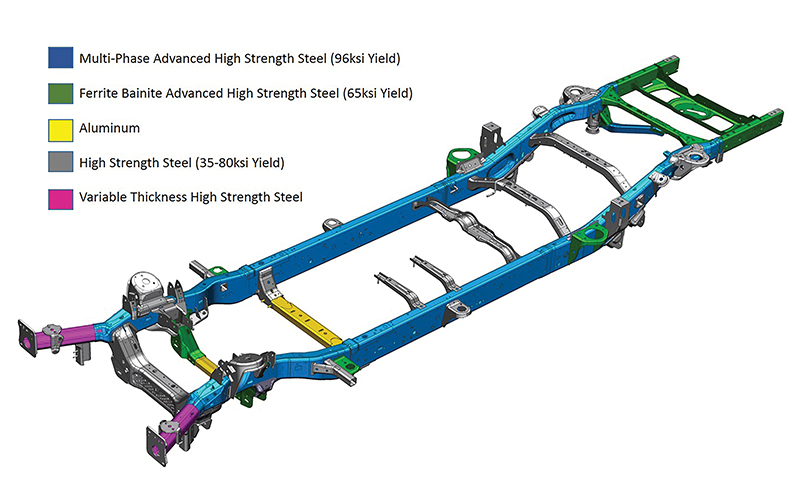
Additionally, a survey by the Steel Market Development Institute found 90% of consumers believe steel is stronger and more durable than other materials used by automakers and 75% regard safety as the most important factor in buying or leasing a vehicle.
The popularity of advanced high strength steel is growing. In 2018, more than 65 vehicles featuring a considerable amount of this material debuted at major auto shows.
According to World Steel Dynamics, the material composite of vehicles is currently seeing a marked change, where advanced high strength steel is surpassing the weighted average per vehicle of mild steel. By 2025, it is predicted that an average of 800 lbs. of advanced high strength steel will be used per vehicle, compared to 300 lbs. of mild steel.
Unfortunately, the elements alloyed in high strength steels can be have deletrious effects to the foundry scrap stream. Common new elements being micro-alloyed in automotive steel include boron, high manganese, molybdenum, and vanadium, along with titanium, cobalt, lead, and zinc. Other rare earths are likely to be added in the future.
Iron metalcasters have already started to see the effect of advanced steel on their incoming scrap charge materials, and extra care and communication will be required to ensure specifications are being met as the trend continues.
Understand Your Scrap Supplier
The changes in steel scrap composition will require extra diligence in understanding operations at the scrap material supplier and communicating to them your foundry’s needs.
“It is critical to know the process in hand at your scrap material supplier to ensure you have the charge materials that fit your needs,” said David Borsuk, manager at Sadoff Iron and Metal Co. (Fond du Lac, Wisconsin).
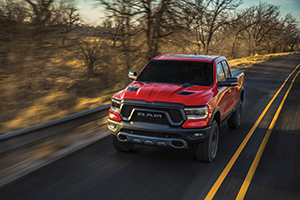
There are two basic grades of scrap: prompt industrial and obsolete. For prompt industrial grades, the scrap supplier should be verifying the chemistry of the material coming from their generators and keep materials that are known contaminants segregated, Borsuk said. A scrap suppliers account representative should have regular meetings with the generators to confirm and reinforce the specifications. And the transportation equipment and containers should be kept clean and inspected as part of the driver’s pre-trip inspection.
Obsolete grades consist of material like farm machinery and demolition scrap.
“It is important your scrap supplier has the material specifications to give to their generators to understand the condition of the materials supplied,” Borsuk said. “They should also have a policy of keeping material out that would be detrimental to health and safety and the environment.”
Borsuk recommends checking with your scrap suppliers to verify they are testing, segregating and documenting material appropriately.
When scrap material comes into the processing plant from the generators, the material should be chemistry tested and then segregated and well identified. After it has been tested and segregated, the material should be visually inspected for potential contaminants, snow and ice, dirt, debris, and nonconforming material. The supplier should also have a maintenance schedule to clean their processing equipment.
When the material leaves the processing plant for delivery to a foundry, the driver should ensure the paperwork matches the material being loaded in the yard. Before being loaded, the truck should be checked to make sure no material has been left in there from another delivery.
“One of the unique things about the relationship between scrap processor and foundry is the partnership,” Borsuk said. “You are not looking at a material transaction but a long term arrangement. Certain things need to be communicated and understood.”
Regular meetings and plant visits will help ensure both supplier and foundry are on the same page regarding specifications and challenges.
Bolster Scrap Testing
With new elements now in the steel scrap stream and no sign of turning back, metalcasters will need to be more careful up front with their incoming scrap to maintain quality standards.
A written specification to the scrap supplier is key. This outlines in detail elements that are not allowed at all as well as the acceptable limits for other elements.
Verifying the incoming material as it is delivered is important. An X-ray fluorescence (XRF) analyzer is a nondestructive tool that can be used to determine the elemental composition. Some metalcasters are now using an XRF gun to check a sampling of every load for steel scrap delivery. Further analysis with a spectrometer in the lab also is important to inspect for elements not easily traceable by an XRF analyzer, such as boron.
Keeping the XRF gun handy, near where the scrap will be delivered, is helpful in ensuring this inspection step isn’t skipped. Extra testing is a little more work, but saves headaches and aggravation in the future.
This article is based on a panel presented at the 2018 Metalcasting Congress, “An Update on the Latest Trends in Ferrous Charge Materials.”
Click here to see this story as it appears in the August 2019 issue of Modern Casting.