From Research to Foundry Application
Kramer Pursell is a metallurgist at Metal Technologies in Auburn, Indiana. He is currently serving as the chairman of the Cast Iron Research Committee, which guides and conducts research for improving and developing cast iron technologies. Modern Casting caught up with Pursell to hear more about the latest projects being conducted by the committee.
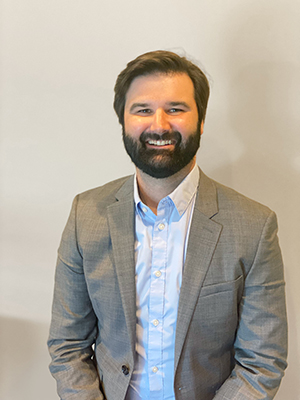
Modern Casting: What’s your role in the Cast Iron Research Committee and how did you get involved?
Pursell: I joined the Cast Iron Committee as a member at a meeting at AFS HQ in 2018 and became Secretary-Elect about a year later. With a lot of movement in the industry during COVID, I moved up the rotation quickly to fill open positions and took over as chair in May 2022. The high level of experience of the committee members and support from the committee made the quick succession much easier.
MC: What is a recent contribution the committee has made to membership and the industry?
Pursell: We’ve guided a few research projects done by terrific PIs. One such project took place at the University of Michigan, where the investigators developed a model to quantify and visualize an accurate representation of the reduced environmental impact of using ductile iron castings over other types of castings and fabrications. Another project from the University of Northern Iowa is providing data on ceramic sands and the resulting casting properties, which is an interest to many foundries as we work to reduce the amount of respirable silica throughout our processes.
There are several other ongoing studies that have direct applications for our foundries and suppliers. The group has really set a focus to make our technical research projects more transferrable into application through interactions with other AFS committees. Another contribution of the committee is applying our technical expertise to guide ASTM and ISO activities to ensure our foundries are represented and kept informed. I am incredibly appreciative of the folks in the committee who take our concerns and solutions to those groups to fight our fights in the international arena because the standards affect us all.
MC: A new iron research project was just approved. What’s the general overview of the project and how can the iron casting industry potentially benefit from it?
Pursell: Yes, thank you for asking about the new project! The Research Committee and team at Missouri S&T recently completed a study on the effects of boron in gray iron, which won the Howard F. Taylor Best Paper Award at this year’s Metalcasting Congress, and we saw a need to apply and expand the experimental procedure into ductile iron. Boron is detrimental to ductile iron because it weakens the high strength grades. The team did some outstanding innovative analysis during the study in gray iron and recently added new state-of-the-art equipment to their capabilities that will help determine how boron acts during solidification of ductile iron. We have high hopes this understanding will lead to theories and trials to mitigate the effects and allow foundries to better deal with elevated boron levels coming from recycling high strength steels and machined chips/turnings and leaching from new furnace linings.
MC: How can someone become involved in the committee? Are there specific areas of expertise the division is looking for in a volunteer?
Pursell: Anyone interested should attend a meeting of one of the cast iron committees. They can reach out to AFS to get onto the email distribution list to be notified; meetings are typically in January, May, and September. Everyone has a different perspective, and every foundry operates a little differently, so we’re looking for anyone who is passionate about moving the industry forward to join. The diverse perspectives and solutions are a strength we need to leverage to keep cast iron as a material of choice in the future. I’d especially encourage people new to the industry to join. It can be overwhelming at first; but personally, being in a room of industry experts with 20, 30, 40+ years of experience in the technical side of cast iron, and the resulting network I’ve formed, has shot me ahead in my abilities as a metallurgist.