Pouring Multiple Metals? Here’s 7 Things to Remember
From training to marking alloys, there are many ways for metalcasters to succeed when working with different alloys and metals.
No metalcasting business is simple. Every facility has its challenges to overcome while striving to produce quality components for customers. Some of them pour multiple metals under the same roof, which presents its own unique hurdles.
Modern Casting spoke with two experienced metalcasting professionals to find out how facilities can succeed when working with different materials.
David Laude is the foundry administration manager at AFS Corporate Member Manufacturer’s Brass & Aluminum Foundry (Blue Island, Illinois). MBAF pours 300 and 500 series aluminum, along with tin bronzes, aluminum bronzes, manganese bronzes, silicon bronzes and high conductivity copper; and grain refined 700x nickel-zinc-aluminum bronze for the glass mold industry.
Also consulted was Tom Doré, the AFS Technical Director. Doré was formerly a vice president at AFS Corporate Member Alu-Bra Foundry (Bensenville, Illinois), where he worked from 1993-2017.
1. Identifying Alloys And Parts Is Crucial
“We have labeled carts for each alloy we pour that we use for each alloy for returns. For ingot, we keep the brass in its identified shipping box until we put it in the crucible to melt. For aluminum, we color coordinate the ingot and the returns carts for each of the aluminums we pour.”
—Laude
“Crucibles have metal tags that travel with them (on them) identified by the alloy they are dedicated for. Any lids or physical covers are cleaned to not have contaminants that can drop in the melt. Ingot skids and containers are identified by alloy at all times. Foundry re-melt container/carts are identified by alloy. All skimming tools, lances or other products that may touch or enter the melt are dedicated or cleaned and identified by alloy type. Barriers may be placed to prevent spills from being comingled between adjacent lines with differing alloys.
“Spills are collected in pans identified by alloy until deposited in the specific re-melt dedicated container. Containers and carts are covered at critical areas like cutoff to avoid incorrect inadvertent additions. Final inspection containers are separated by dedicated barrels. Sample chemistry is checked and matched to customer, part, order and melt lot.”
—Doré
2. Production Planning Can Be Optimized
“Each morning the production schedule is communicated to each department so they have an idea of what alloys will be poured that day. We try to plan it so the molding changeover happens around the same time as the furnace changeover so the molds aren’t waiting for metal. What helps is the induction furnaces we use have a capacity of 100-200 lbs. of aluminum, so changing to a new alloy isn’t too much longer than staying on the same alloy.”
—Laude
“Production is planned based upon the product mix, demand, due dates, alloys, molding rates, melt rate, and time impact to prepare crucibles and melt staging for alloy changeovers. It is a complicated plan to optimize properly. Sand requirements are planned and the molten metal heat impact on overall sand system quality is considered. When a pattern is used for multiple alloys the pattern dimension needs to consider the effects of pattern shrinkage relative to dimensional requirements. The gating and rigging design needs to accommodate all alloys that may be run through the gating system, including differing venting and chilling requirements, and the impact different metal temperatures may have on core gas evolution. The accommodations to pour multiple alloys from the same tool frequently have an effect on cost optimization.”
—Doré
3. The Melt Room Is A High-Risk Location
“It’s going to catch the sum of how well you’ve controlled your contamination efforts throughout the foundry. In many foundries, the different alloys are running concurrently, so there may even be multiple plates producing the same part in two different but similar-looking alloys. But there would be severe consequences with a mistake.
“If you’ve controlled everything all the way through, and at final inspection somebody finds a defect and the casting is rejected and it’s tossed into the wrong barrel to be returned for re-melt, multiple heats can be contaminated. The melt room is the key.”
—Doré
4. Training Must Take Place Throughout The Facility
“It starts with leadership ensuring all carts used for returns are always labeled. This is critical when we have a low yield job and run out of identified carts for that given alloy–we must stay on top of any temporary usage carts. From there, we must train all employees on the importance of segregation of alloys. We follow our ISO 9001 quality procedures and make sure we do what we say and say what we do, and keep all of our operators trained on any and all changes that are made.”
—Laude
5. Molds Are Also Affected
“Let’s say you’re a predominantly aluminum foundry and you’re going to run some brass castings, which are three times more dense than aluminum and have a higher pouring temperature. Your mold-to-metal ratio may matter more now, and the properties of the green sand will have to be monitored.”
—Doré
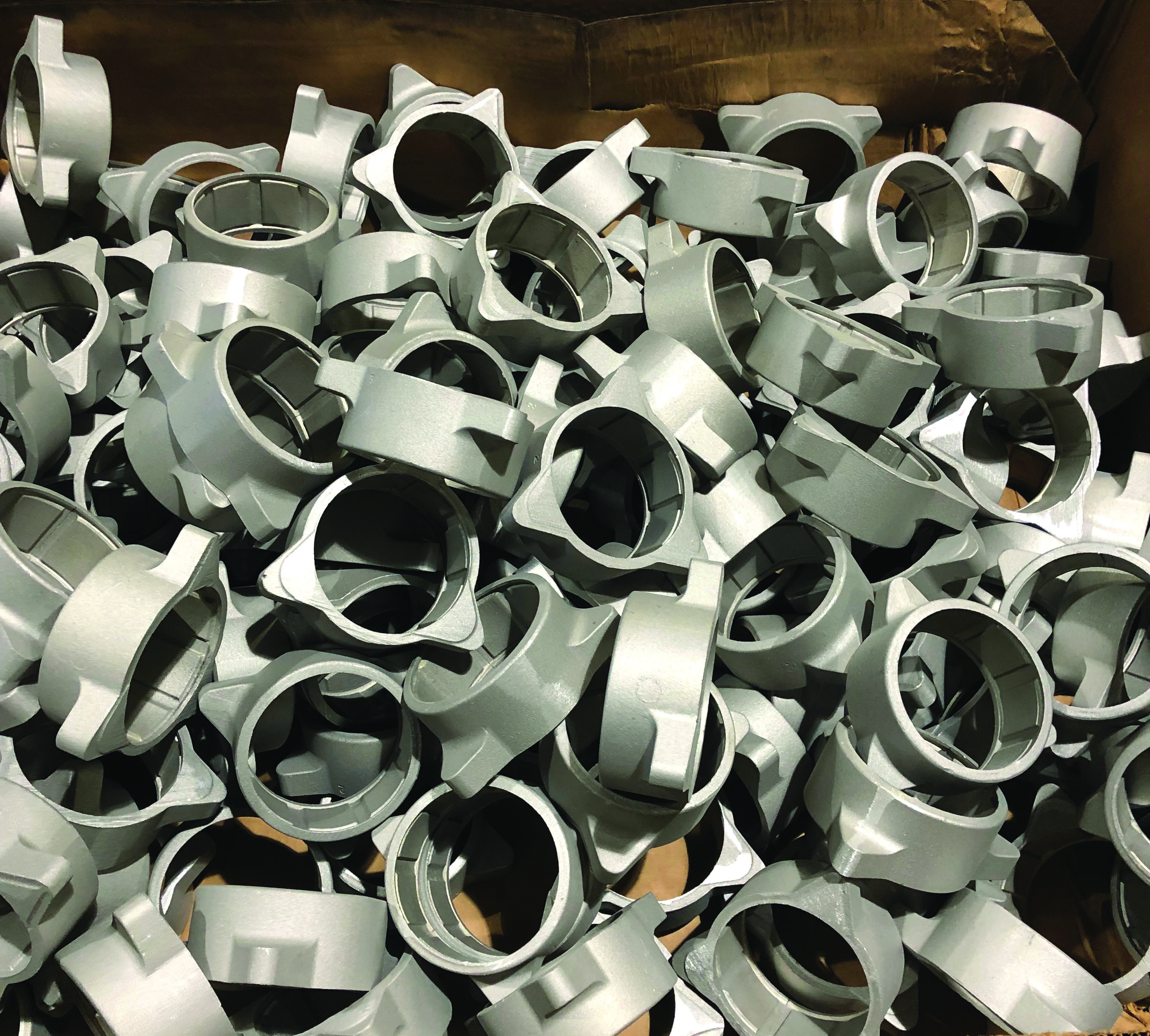
6. Preheats Can Help
“At the end of the day, we usually know what we’ll be pouring first thing the next morning, so we’ll get that alloy near the furnace area and get it so the furnace is ready to turn on. When changing over, we try to get the next alloy crucible ready and turn the furnace on so it is heating up as we are pouring the last pot of the previous alloy.”
—Laude
“Generally, I like to preheat early before the production lines are filling to avoid bottlenecking once molding has begun. I prefer to try to keep each alloy running all day or until it may be completed and a currently running alloy can be expanded over to the furnace to continue pouring.”
—Doré
7. Avoid Contamination
“For anyone who’s running multiple alloys, the biggest consideration is to avoid cross-contamination. To do that, foundries may need to choose a dedicated crucible for each alloy. But if a facility is not set up in the kind of environment to be able to do that, extreme care and consideration needs to be taken on how the crucibles are cleaned, because that can be a source of contamination.
“Every employee needs to understand the consequence of contamination to be on alert for potential mistakes and mistake opportunities. In case of doubt, the metal must go into the identified scrap barrel that can be sent for separate recovery operations.”
—Doré
Click here to see this story as it appears in the September 2019 issue of Modern Casting.