Foundry meets OSHA silica PEL with dry venting
After purchasing a foundry, the new owners wanted to invest in the business by improving production and making the facility safer for their employees.
At the initial site visit, AFS Corporate Member Schust Engineering (Auburn, Indiana) was called to help replace an older wet scrubber dust collection system that was showing its age. Because the wet scrubber was struggling, the facility was risking compliance with emission standards. The company was also looking to expand production in conjunction with replacing the wet dust collector.
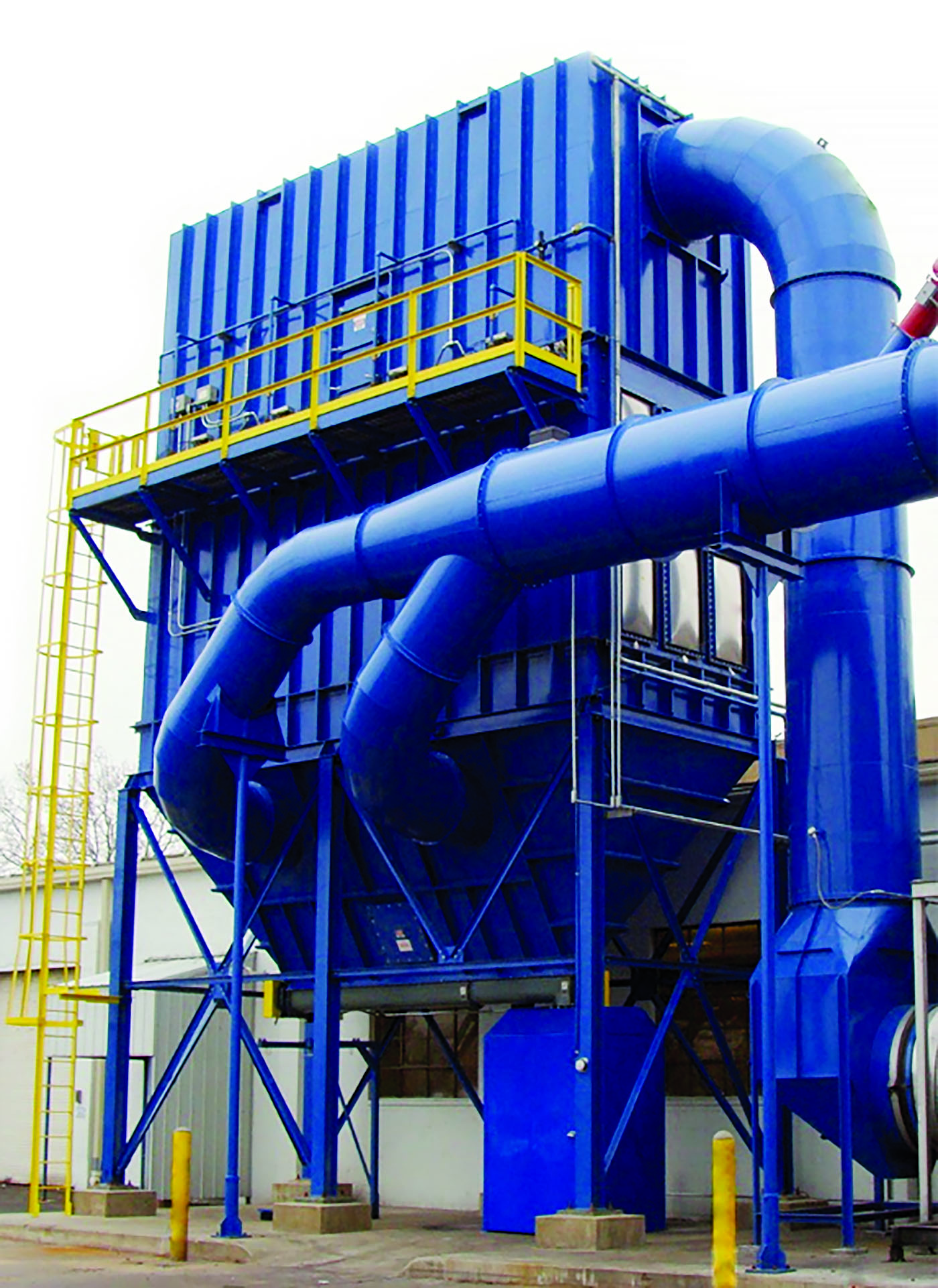
Schust recommended a plant ventilation audit to understand the process and equipment involved. In conjunction with the audit, Schust also conducted an engineering study to ensure the right solution was being put into place to support the transition from wet to dry dust collection and consider the needed production expansion.
Getting the facility operating with lower emissions was the main priority while designing and engineering the new dust collection system. Within three weeks, Schust fabricated and installed new 12-gauge mild steel ductwork from the existing wet scrubber to a new fan inlet.
Because the duct was temporary, Schust used lighter and economical gauge material to keep the facility in compliance. Shortly after this, the foundry ordered a new pulse-jet continuous automatic dust collector. A new duct was installed from the dust collector outlet to the existing fan inlet duct. The online cleaning system was designed to include bags, cages, platform and ladder, and a screw conveyor and rotary valve. To complete the retrofit from a wet to dry process, Schust supplied and installed the compressed air piping and included filter/regulator, unions, and necessary shut-off valves.
A screw conveyor and airlock are used at the bottom hopper of the pulse-jet dust collector to remove the dust collected on the bags. As the bags are cleaned, the dust falls from the bags, is augured through the screw conveyor and discharges through the airlock to a disposal tub. Schust provided engineering, fabrication, installation service, and engineering field service for the new pulse-jet dust collector, which replaced the wet scrubber and supported expansion at the foundry.
About a year and a half after the initial installation of the single dust collector module system for the facility’s sand system, the business saw tremendous growth.
Since then, the foundry has added three more modules, two large fans, one common stack, control room, and new system control panel. The Schust system then and today meets the new OSHA respirable crystalline silica regulation.
Click here to see this story as it appears in the July 2019 issue of Modern Casting.