Committee Q&A: Kirk Rogers
How can cutting-edge technology be introduced and integrated into a centuries-old industry? One effective way is through association membership, and it’s how Dr. Kirk Rogers—additive manufacturing (AM) expert—became involved with AFS.
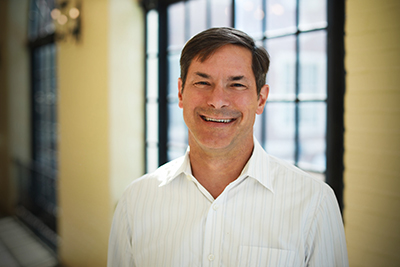
Rogers has used additive technologies to solve manufacturing, repair, and supply chain problems for the last 10+ years. He began consulting full time in 2018 after leading the technical team in startup of a $40 million Additive Manufacturing R&D center. At the center and since, he has specified, defined, and executed AM projects with more than 100 organizations in diverse industries that use castings. Rogers was an FEF scholarship recipient in 1989 and is outgoing chairman of the Additive Manufacturing Division.
Modern Casting caught up with Rogers to talk about his experience with volunteering on AFS committees.
Modern Casting: What’s your role in the division and how did you get involved?
Kirk Rogers: I’m the Additive Manufacturing Division Chair until rolling off the leadership at Metalcasting Congress in the spring. I became involved in 2015, when we installed an ExOne sand binder jet printer at an Additive Manufacturing Center of Excellence at GE in order to help GE companies advance additive-enabled castings to solve some supply chain challenges. I enrolled the center to become an AFS Corporate Member and joined the Ad-Hoc Additive Manufacturing Committee at the time. As the committee became a division and established leadership structure, I volunteered. When I left GE to start consulting, I maintained my individual membership.
MC: What is a recent contribution the committees/division have made to membership and the industry?
Rogers: One of the most significant things the Additive Manufacturing Division has provided is a publication from the sand committee to help companies understand the advantages of 3D-printed sand tooling and nuances in using it to make complex castings. (The guide, “The 3D Printed Precision Sand Casting Process,” is available for purchase at
https://bit.ly/3IWNLkU.)
MC: What foundry issues is the division tackling right now and how?
Rogers: We are just wrapping up an AFS-funded project comparing dimensional accuracy of castings produced by conventional molding and cores versus 3D-printed sand. It’s a reasonably complex casting with some difficult features, so I’m expecting the results will open a lot of eyes in the industry. The Hard Tooling Committee and Lost Foam Division are also working on a project on lost foam tooling produced by several different additive manufacturing processes in order to increase the speed at which tooling is available and reduce cost of that process. It’s been delayed a bit by job changes and operational availability in participating foundries but should have some good final results soon. I expect that tooling in less than half the time and half the cost of conventional tooling will garner some industry interest!
MC: How can someone become involved in the division? Are there specific areas of expertise the division is looking for out of a volunteer?
Rogers: We would love active participation in the committees! Please reach out to me, kirk.rogers@case.edu, or Travis Frush, tfrush@afsinc.org, who was recently named AFS technical representative to our division. We have great participation and lots of good ideas from consultants, and suppliers but are really looking for operating foundries that want to participate in 3D printing for molds and tooling or are interested in direct metal printing. We have two active committees, 3D Sand Printing and 3D-Printed Hard Tooling, and a task group focused on standards and specifications.