University metallurgists awarded second $2 million grant
A Missouri University of Science and Technology research team was recently awarded a $2 million grant from the U.S. Department of Energy to research technologies to improve the operating efficiency of electric arc furnaces (EAFs) used for steelmaking.
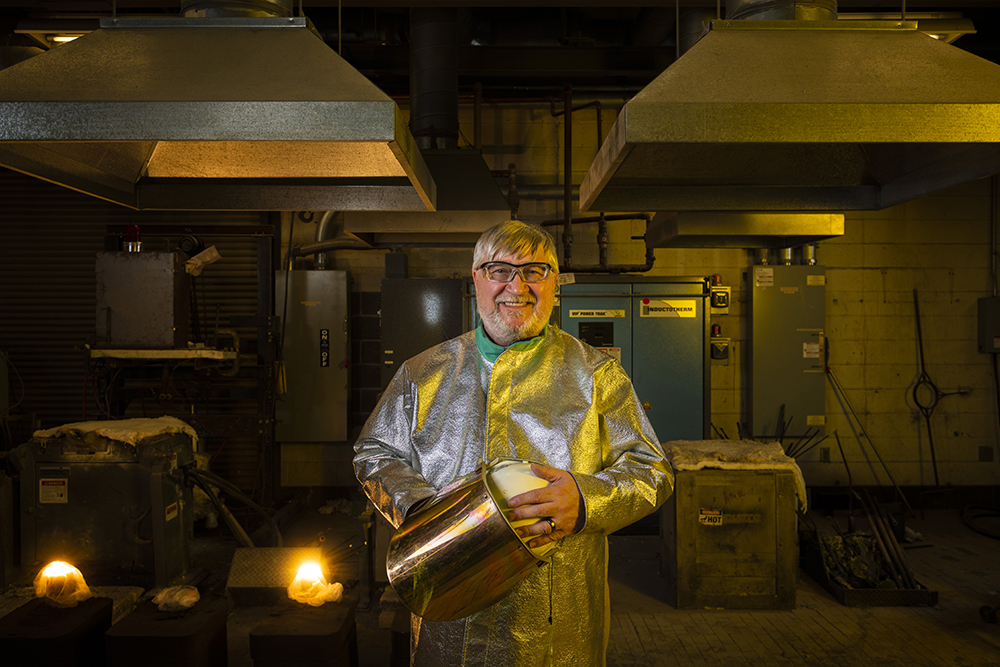
“It takes a tremendous amount of power to run an EAF, and we are looking for new ways to lower that energy footprint,” said Dr. Ronald O’Malley, the F. Kenneth Iverson Endowed Chair of Steelmaking Technologies and director of the Kent D. Peaslee Steel Manufacturing Research Center at Missouri S&T. “We are working toward implementing a next-generation dynamic control system for the EAF so we can optimize EAF operating efficiency under changing input conditions using new sensor systems.”
The project is titled “Intelligent Dynamic EAF Advisory System (IDEAS) for Improving EAF Operating Efficiency.” The grant is part of a larger three-part project: Phases 1 and 2 were both funded with approximately $2 million awarded in December 2022. Phase 3 funding of over $1 million is expected to be distributed next year.
For the first phase, the research team assessed the current systems in place at the two steel plants that are partners in the study and developed the conceptual framework for the future aspects of the project. This stage required significant data analysis for the process, integration of existing control modules already in place, implementation of new control modules, and development and testing of new fiber optic sensing technologies in the lab for use in the EAF.
In Phase 2, the new fiber optic sensing technologies will be implemented in the plants along with new control systems, directed energy input and EAF slag property models.
“In basic terms, the fiber optic system will provide a whole new set of tools for EAF optimization,” O’Malley said. “We will be able to better examine the condition of the EAF and the impact of operating variables on the process in real time to provide feedback to the operator and improve energy efficiency, operating cost and yield.”
The new sensor technology and control modules will be installed at the partner steel plants, Big River Steel in Osceola, Arkansas, and Commercial Metals Company (CMC) in Birmingham, Alabama.
After that, the systems will go live, and the data collection process will begin. Throughout the process, the plant employees will be trained on how to use the new technology as well. Then, in the final stage, the researchers will analyze the performance improvements in progress and determine what changes should be implemented to further improve the system.
“Something people should also appreciate about this project is the benefits to the student researchers involved,” said O’Malley. “S&T and ASU will have a team of undergraduate and graduate students working on this project. You can’t beat the hands-on experience that this will provide for our students.”
In addition to Big River Steel and CMC, other research partners include CIX, ASU, Nucor Corp., Linde and Gerdau.