Q&A With Julia Jones, Newport News VP of Manufacturing
Modern Casting’s Kim Phelan visited with Julia Jones one October afternoon and the Newport News Shipbuilding vice president of Manufacturing offered a closer look into her company’s foundry and culture.
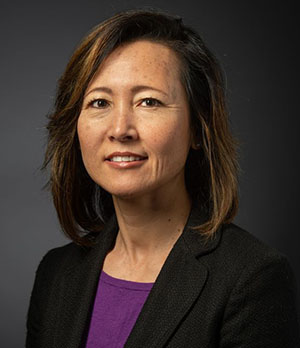
Modern Casting: Can you give us a picture of the collaboration between the foundry engineering group and the shipbuilding design engineers—and what about foundry interface with the Navy customer?
Julia Jones: We do have designers and engineers on site in the foundry team, and the closeness and tight collaboration across the internal organization for the work that we do happens every day. For example, they collaborated when the new technical requirements came out from the U.S. Navy.
They’re looking for ways to make not just the process operations efficient, but also in solving technical problems that the Navy’s design team may have. And a prime example of that is on the Virginia class submarine, which we’re building now, where the team collaborated to improve throughput of our production work. And this was recognized as our annual model of excellence that is awarded by the president of the company. So, there’s definitely collaboration, but it goes even beyond us in that our engineering and our chief engineering officer are tightly linked to the Tech Warrant Holder who provides Navy governance and guidance on design. It truly is a sort of seamless collaboration on how we do our castings.
MC: Let’s talk about safety for a minute. Who is watching out for people in the foundry, and what are your successful techniques to ensure worker safety every day?
Jones: I’ve been here 24 years, and I can tell you, safety has always been Priority No. 1, above all things. We want every single shipbuilder to leave work the way they came in, and not get injured. When you come into an environment like the foundry, first of all, not everybody has worked in a foundry before, and because of that, we have same level of safety precautions and measures in place from the first day that a new hire starts to every day and how they conduct their work.
Every single day there’s a crew huddle—the frontline supervisor and every team member will huddle just before they start their shift. They’ll talk about what has to get done for the day. What are some safety learnings from the day before that they want to be mindful of—we want to share any near misses if there are any, or if there’s something that someone has identified. So, there’s good conversation happening as a pre-job brief prior to going to work.
Infrastructure wise, air pollution control systems are all maintained; every piece of equipment has an operator daily checklist that gets conducted before we operate the machinery. In terms of each individual, there’s PPE they have to wear—their hard hats, their glasses, their shields and gloves, and so on.
We do have an extensive safety training for all employees and repetitive training that everyone has to take periodically just to keep all the safety measures in place. That’s definitely where we spend a significant amount of time.
And before we do a pour, we do a mock-up drill several times to make sure everything’s going according to plan. Everybody knows what needs to happen every step along the way. And they’ll work through any hiccups prior to doing the actual pour, which can be anywhere from 38,000 lbs. to 110,000 lbs. That’s one of those times where I say it’s good to slow down a little bit and do those drills. It is a very well orchestrated activity within the foundry team.
MC: It can seem patronizing to make a big deal over women in industrial leadership, but it is refreshing to see a healthy representation of female leaders in a traditionally male-dominated industry. Can you share some personal thoughts about this dimension of the NNS culture?
Jones: Jennifer Boykin is the first female president in NNS history. I, on the other hand, am not the first VP of manufacturing. But I’ve been in the company 24 years, and we’ve come a long way—I don’t mean like from caveman stage to astronaut, but I have seen a positive progress in our culture.
If you don’t know shipbuilding, you may think it’s very archaic. You may think it’s a very male-dominated world. But at NNS, we have a long-term strategy that we called NNS Forward Strategy, and our entire 25,000-plus shipbuilders are rallied around it. Elements of that strategy are tied into our five pillars: how we enable our workforce, how we transform our business operations, how we execute efficiently, how we grow our business base, and last but not least, is leading the way. It’s all about leadership, and the central element of leadership is in who we are and how we do our work.
One other thing I want to share about the foundry because I’m so proud of it: We have a foundry women’s council that got set up a couple of years back. Through our many Gallup surveys and our Forward Strategy, we have heavily focused on inclusion and diversity engagement. So we’ve focused on hiring and looking for people that are interested in becoming a shipbuilder, but particularly into the foundry, which is a small group and not as diverse. But now, 10% of the foundry team are women in different roles. And they took the initiative to create this foundry women’s council because they want to bring others into these roles. Most people from outside our business would think, ‘Oh no, I can’t do that job.’ But that is not so.
MC: What do you consider the No. 1 challenge facing the NNS foundry? In other words, this is the “what keeps you up at night” question.
Jones: What keeps me up at night, both for the foundry and for rest of my manufacturing shops, is safety. I want to make sure that every single individual is safe.
My heart starts racing a little bit when we’re doing pours—not because I don’t have confidence in the team, but really it’s in a split second that something could go wrong. Safety by far is what keeps me up at night.
In terms of a big challenge, it’s not so much a new challenge, but it’s our mission to support the U.S. Navy. And as they continue to require ships and maintenance of ships, we are fully committed to delivering those on time, which means we have to keep up with work that we have committed to do for them. And we’re doing that very well in terms of making the pours on time and delivering the products downstream where the work needs to get done. So, it’s not a challenge as much as keeping up.
MC: What are your goals for the foundry over the next 12–24 months?
Jones: It’s real simple for the next year or two—my focus for the foundry as well as for the rest of the manufacturing area is to really strengthen our capabilities that we have and make the right investments in building up that capability.
Also, to continue supporting the U.S. Navy. There are new Tech Pub 300 requirements, which are slightly different requirements than what we’ve been used to in the past. So we are making investments in assets. But if there are additional investments needed, I want to make sure that we are focused on doing that so we can deliver good quality castings on time.
We do have a capital plan that we revisit every year. That looks out for the next five years, which is more than just the foundry—it’s across the entire shipbuilding operation. It’s about investing in things like additive manufacturing, and what is that role, as well as infrastructure upgrades.
Because there are advancements in technology, there are better tools and better equipment out there, and so we have to make smart decisions on what those investments would yield. We’ll work collaboratively across the board to decide what makes sense and what gives us the best bang for the buck in terms of being able to deliver the products on time.