EJ Wins Metalcaster of the Year
The northern Michigan company invested heavily in a new state-of-the-art facility, showing its commitment to its core customers and the whole industry.
When AFS Corporate Member EJ broke ground on its new metalcasting facility in February 2017, it was an important milestone for the company and its commitment to its future and the industry as a whole.
The plant, in Warner Township near Elmira, Michigan, signaled the beginning of the company’s next era in its northern Michigan home. EJ is a privately owned business with members of the fourth and fifth generation of the Malpass family actively involved in the operations. The corporate headquarters are in East Jordan, Michigan, where the company was founded over 135 years ago.
By modernizing its operations, EJ was illustrating its investment in the future. It decided to transition to electric melting and discontinue producing brake drums, while focusing on EJ’s core products: access solutions for water, sewer, drainage, telecommunications and utility networks.
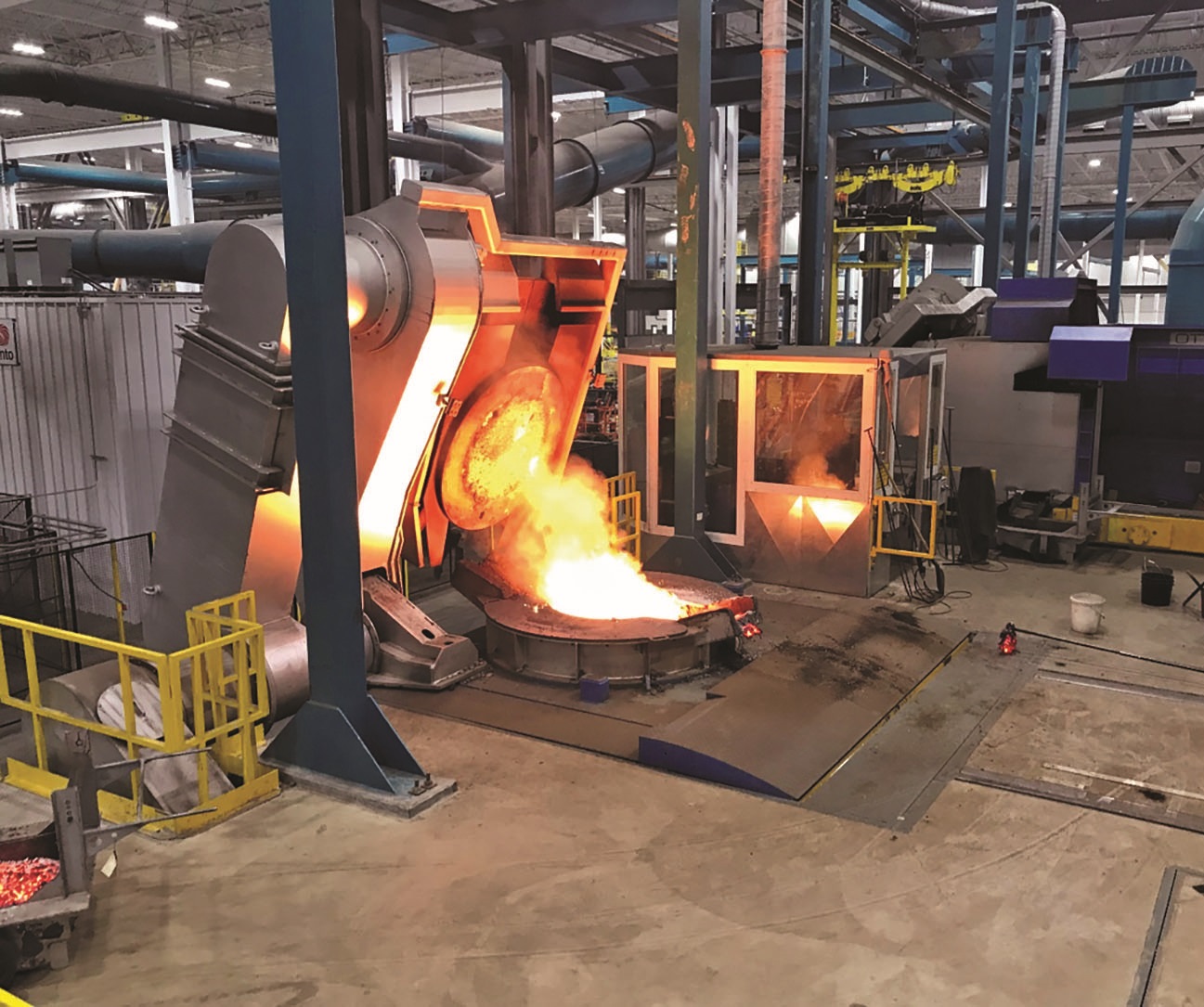
Two years later, the sprawling plant covers 7 1/2 acres on a 200-acre plot of land and is fully operational as the company was able to keep its 340 employees working. At the intersection of US Highway 131 and Michigan State Highway 32, the modern facility rises out of the northern Michigan landscape. Efforts to buy the land and power the facility were successful. Inside, the lights are welcoming and bright, and much of the equipment is brand new.
“Everyone is really pleased with the outcome of the new foundry. The construction of the new foundry represents the single largest investment in the history of EJ,” said Tom Teske, vice president and general manager of the Americas for EJ. “We are pleased we have a family group of shareholders with a long-term view of investing in our business.”
But getting to the final outcome wasn’t easy. It meant continuing production in the older plant while the new one was being completed 15 miles away. Land wasn’t readily available, not to mention land with the right soil to handle a massive new foundry and everything else required. Northern Michigan winters aren’t easy for anybody, let alone construction crews. Finding those construction crews and all the necessary tradespeople was challenging thanks to a strong economy that has kept workers busy.
“There’s got to be a lot of perseverance,” EJ president Tracy Malpass said. “Some things are going to happen, and you’ll have to work your way through them. There’s been a lot of sleepless nights for all those involved in the project, but we’ve learned a lot and are better for it.”
Those sleepless nights, however, are paying off. On October 25, 2018, the company hosted an open house at the new plant, and production is now humming along. For the investment in its future, EJ has been named the 2019 Metalcaster of the Year by Modern Casting.
Making the Move
In September 2016, EJ announced it would be retiring the East Jordan foundry, located there since 1883. The retirement of the operation came with excitement, as employees learned the company would build a new, state-of-the-art foundry just 15 miles away.
The shift to more modernized operations and staying close to its original location are examples of the company’s dedication to growing the business, servicing its customers, and the importance of retaining a dedicated and loyal workforce.
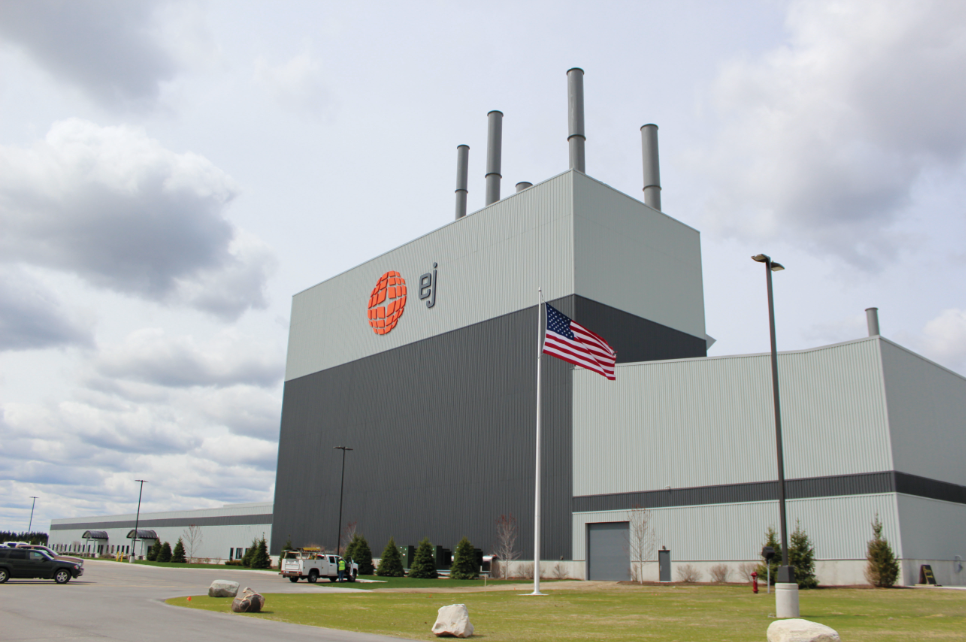
“Once the decision was made to build the new foundry, communication to our employees was our top priority,” Malpass said. “Our leadership team carefully planned the communication to all employees. During the construction and move, multiple videos, pictorial updates, pamphlets, and meetings were used to keep employees informed. We were excited about the project, and we wanted to ensure our employees were informed and excited too.”
“When the move was announced, we conveyed why,” said Mark Aepelbacher, director, cast products. “We needed to keep our employees informed, all while ensuring that we continued to support production and safety at our original foundry in East Jordan.”
As Aepelbacher mentioned, EJ not only took on a large construction project, but continued operations at its East Jordan facility until the move was completed. This allowed the company to continue providing for its customers and maintain jobs for its employees, so they could shift to their new work location.
The project started with the complicated task of securing land. The property required certain soil conditions, access to roads, power, well water, and the correct permits, among other necessities. The process to find land within 15-20 miles of East Jordan, which was expected to go quickly, lasted nearly six months.
Purchasing the land was one aspect but getting power to the site was an additional challenge. Due to the transition to electric melt, standard power would not suffice. Connecting a nearby high-voltage electrical distribution line required EJ to work with site neighbors to acquire additional property and easements.
Once the land and power were taken care of, EJ had to get around to another task: building the facility.
“The design and equipment selection phase was exciting,” said Todd Ingalls, director, facilities engineering & support. “We were tasked with selecting equipment that would support our environmental and safety expectations, as well as increase our efficiencies.”
PHOTO GALLERY: EJ wins 2019 Metalcaster of the Year
While designing the foundry, EJ focused on environmental responsibility. Since a high amount of environmental controls are at this site, the environmental impact is reduced. The air pollution control equipment is highly efficient, the melting equipment does not use fossil fuel, and there is no release of process or non-contact cooling water from the facility.
The company also worked to reduce noise and lighting while controlling storm water.
To help plan the facility and manage the project, EJ turned to AFS Corporate Member Kodiak Group, which partnered with EJ’s Facility Engineering Support team to design the process flow, engineer the building, and manage the construction of the project. AFS Corporate Member Simpson Technologies supplied the sand mixing and cooling equipment, fellow AFS Corporate Member Otto Junker designed and installed the electric melting and pouring system, while AFS Corporate Member Sinto was responsible for the new green sand molding line and relocating an existing molding line from the old foundry to the new one. AFS Corporate Member Haley & Aldrich was selected for environmental design and permitting.
Many of those names had worked with EJ on their Ardmore, Oklahoma, foundry that was completed in 2001. That familiarity helped, as did the experience of having built a foundry within the last 20 years.
Though the support from vendors and suppliers was key, finding construction and tradespeople to erect the building proved to be difficult. Given a strong economy, construction crews were somewhat difficult to find, and they also had to be prepared to build through the tough Northern Michigan winters.
Malpass estimated construction productivity during the winter months was about half of what it normally would be, given the weather. EJ kept safety top-of-the-mind and made decisions to support the safety of the construction crews and their own employees. Wind gusts meant cranes would be shut down, temporary walls and heating were added to protect crews from the elements, and safety features were added to prevent hazardous working conditions.
Keeping It Going
To keep the business moving forward, EJ built up inventory prior to transitioning to the new facility. It also relied on the Ardmore location to ramp up production to cover customer demands.
That wasn’t the only challenge the company had to beat.
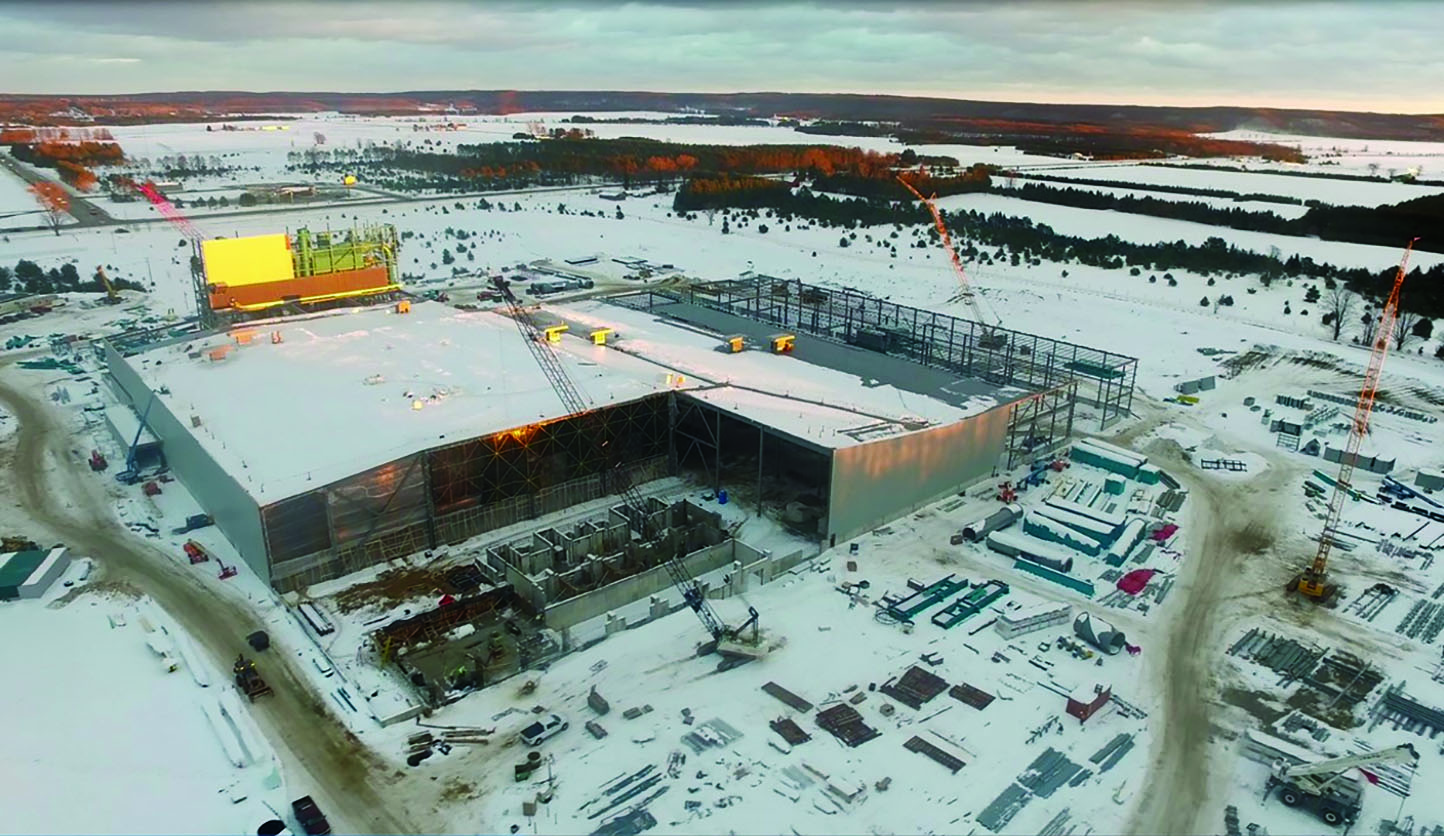
“Once the transition started to the new foundry, we faced some challenges simply learning the new operation. The two most difficult challenges were starting up on 20 hours of production per day and the change from cupola to electric melting,” said Scott Nachazel, facility manager. “Our employees have been resilient and willing to learn new processes and procedures.”
Teske echoed that sentiment, and made it clear what the new building says about EJ’s future.
“This new foundry demonstrates that we have the capacity to supply high-quality products to U.S. markets while protecting worker safety and doing so with the very best environmental controls available,” Teske said. “It also demonstrates to our customers that we’re committed to being a leader in this industry, that we have unmatched capabilities and resources, and that we’ll be here for the long haul.”
Click here to see this story as it appears in the June 2019 issue of Modern Casting.